Get in touch now
Production technologies
Broad range of technologies offers diverse possibilities

An extensive product portfolio requires numerous production technologies. Thanks to our technological depth, we’re able to provide our customers with objective advice and offer the precise solutions that are ideally tailored to a project’s individual requirements. Following market trends closely is also key for us in the technologies area. This not only lets us integrate innovative processes into our portfolio in a rapid, uncomplicated way – we’re also able to act when special solutions are required. Thanks to this, we’re always positioned to offer our customers state-of-the-art technologies. And we naturally use resources in a sustainable way with all of the technologies we deploy.
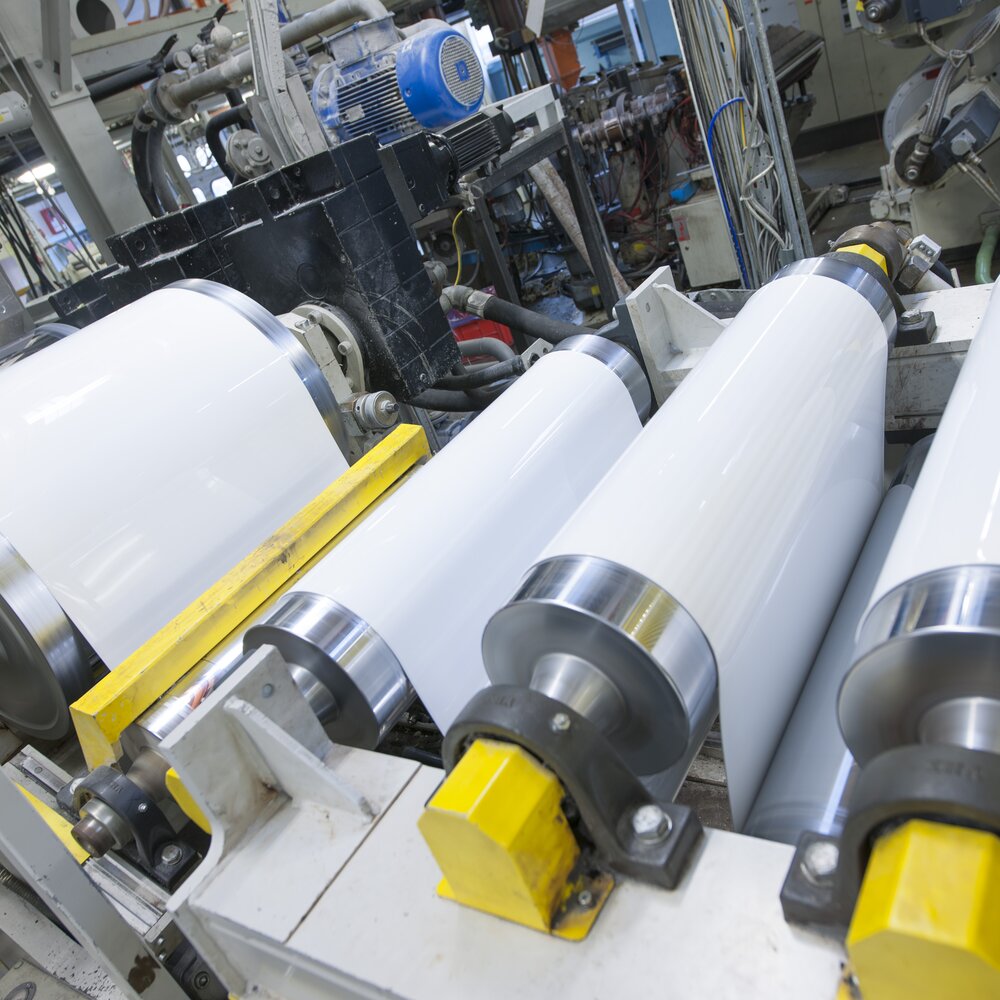
Sheet extrusion
The sheet extrusion process is used to produce sheets which are then processed into packaging – in our case, the extruded sheets are utilized to fabricate rigid packaging solutions. This approach is efficient and cost-effective.
Materials used: primarily PP and PS
Efficient process for a wide range of sheet products
During sheet extrusion, plastic granulate – either new or recycled material – is smelted and formed into a thermoelastic sheet by a shaping nozzle before being wound onto a roll following the cooling process. The plant technology makes it possible to manufacture multilayer sheets. Recycled material can be incorporated in the middle layer.Materials used: primarily PP and PS
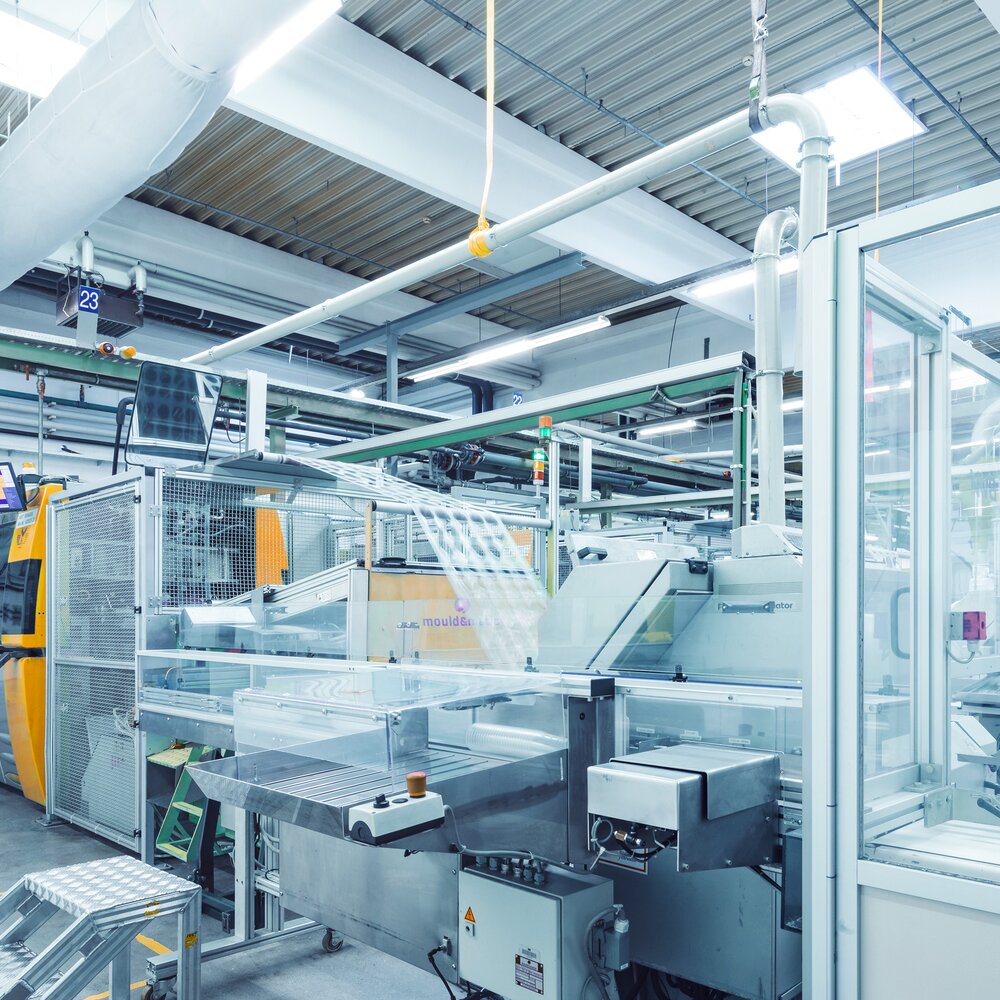
Thermoforming
Thanks to thermoforming technology, it is possible to produce millions of plastic parts cost-effectively and efficiently. An affordable alternative to injection molding, thermoforming is one of the most popular processing methods for plastic packaging, particularly for large series in standard formats.
Materials used: thermoelastic sheets made of PS, PP, PET, r-PET, PE, ABS
Products: yogurt cups, butter tubs, lids, trays, and much more
Economical technology for large series
During thermoforming, extruded sheets are fed into a thermoforming machine, where they are heated. The thermoelastic sheet is then stretched forward in the tool and molded by compressed air, cooled down and punched. The cups are ejected and stacked, then further processed or packed, depending on the respective application. The skeleton sheet is ground right at the machine and immediately incorporated as raw material into the middle layer during inline sheet extrusion.Materials used: thermoelastic sheets made of PS, PP, PET, r-PET, PE, ABS
Products: yogurt cups, butter tubs, lids, trays, and much more
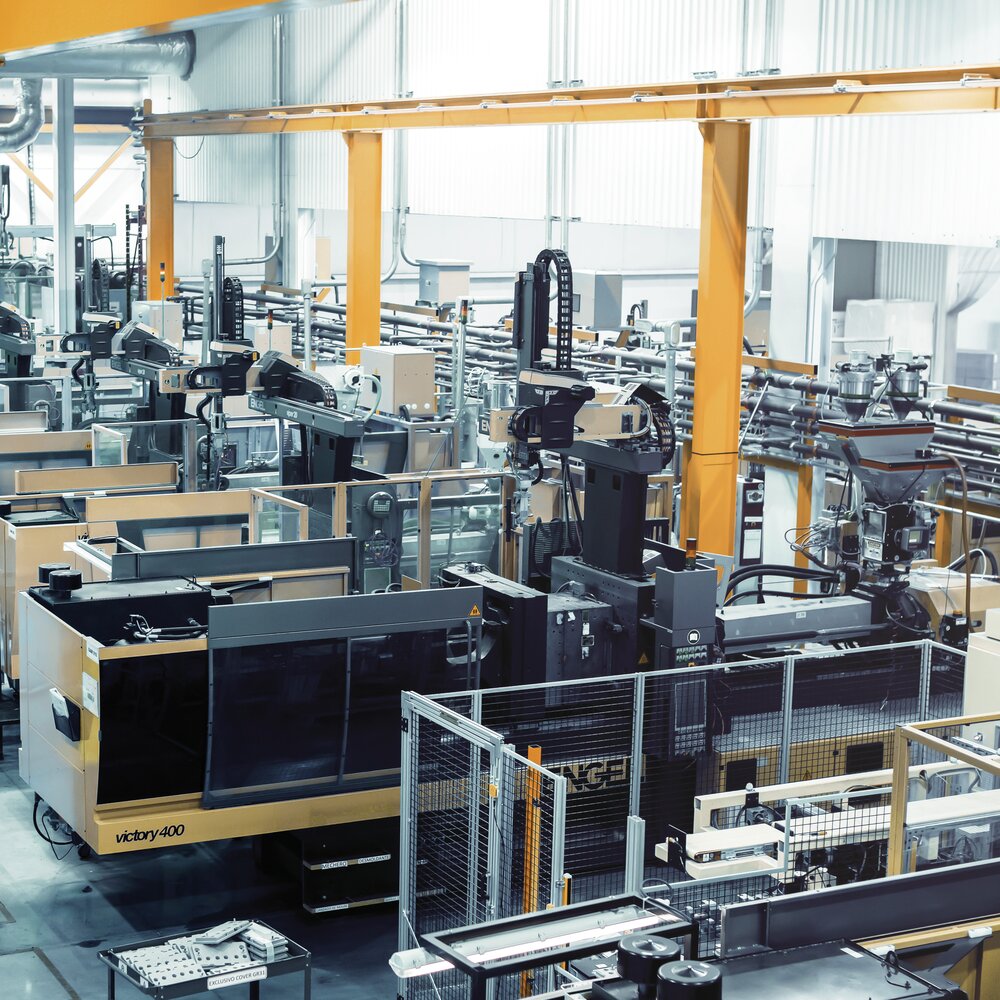
Injection molding
Injection molding is a popular production technology thanks to the wide range of different shapes and surface structures it offers. In the area of plastic packaging, it is primarily used when special design shapes need to be produced in small and medium series runs.
Materials used: primarily PP, PS
Products: yogurt cups, butter tubs, lids, and much more
Proven production method for molded parts of any type
Injection molding is one of the most popular methods for producing plastic parts. Plastic granulate is smelted, injected into the desired shape under pressure, cooled, and automatically extracted or ejected. Almost any shape, even those with undercuts, can be manufactured using the injection molding procedure.Materials used: primarily PP, PS
Products: yogurt cups, butter tubs, lids, and much more
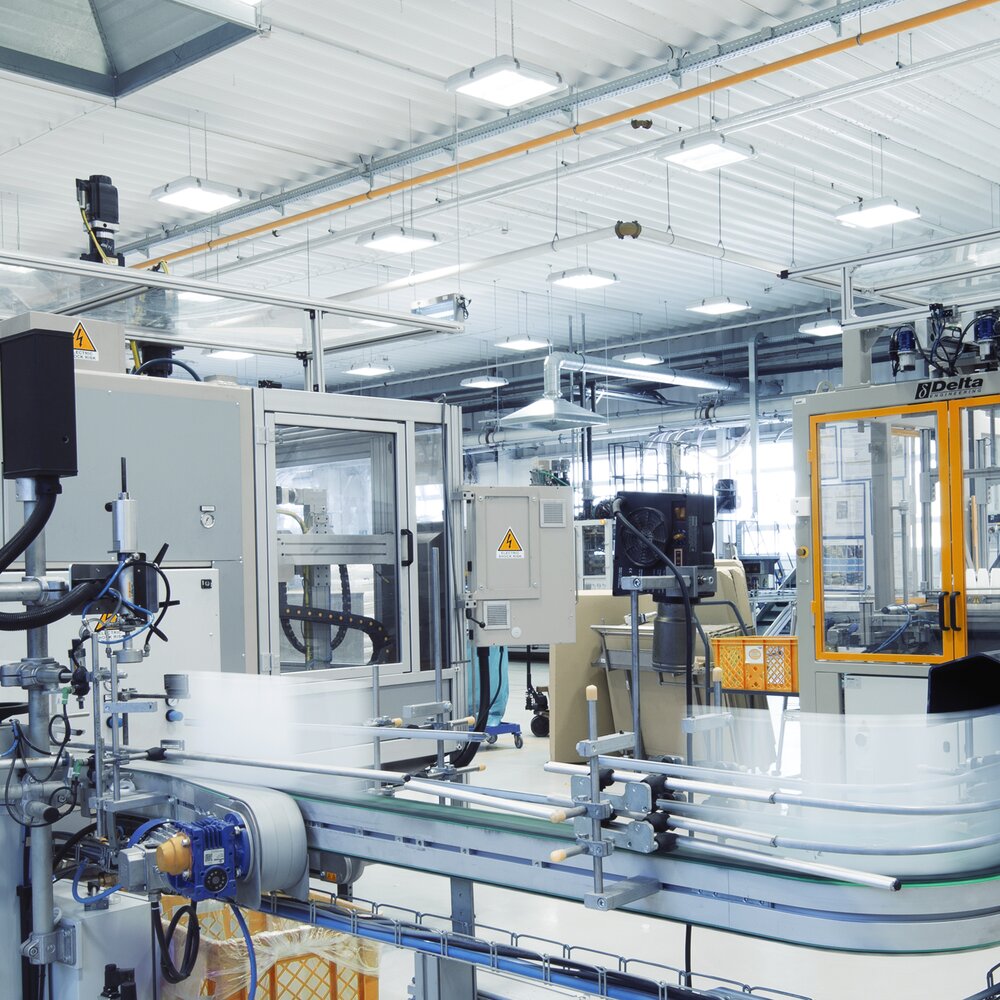
Extrusion blow molding
Extrusion blow molding enables the production of hollow items with very small and very large geometries – catering to volumes from around one milliliter up to ten cubic meters.
Materials used: primarily PE
Products: bottles, canisters, jars
Tried-and-tested method for producing hollow items
When used to produce hollow items, extrusion blow molding makes it possible to implement extreme shapes and designs efficiently. During this process, a tube is extruded, cut off, and transferred to a shaping tool where it is inflated with compressed air.Materials used: primarily PE
Products: bottles, canisters, jars
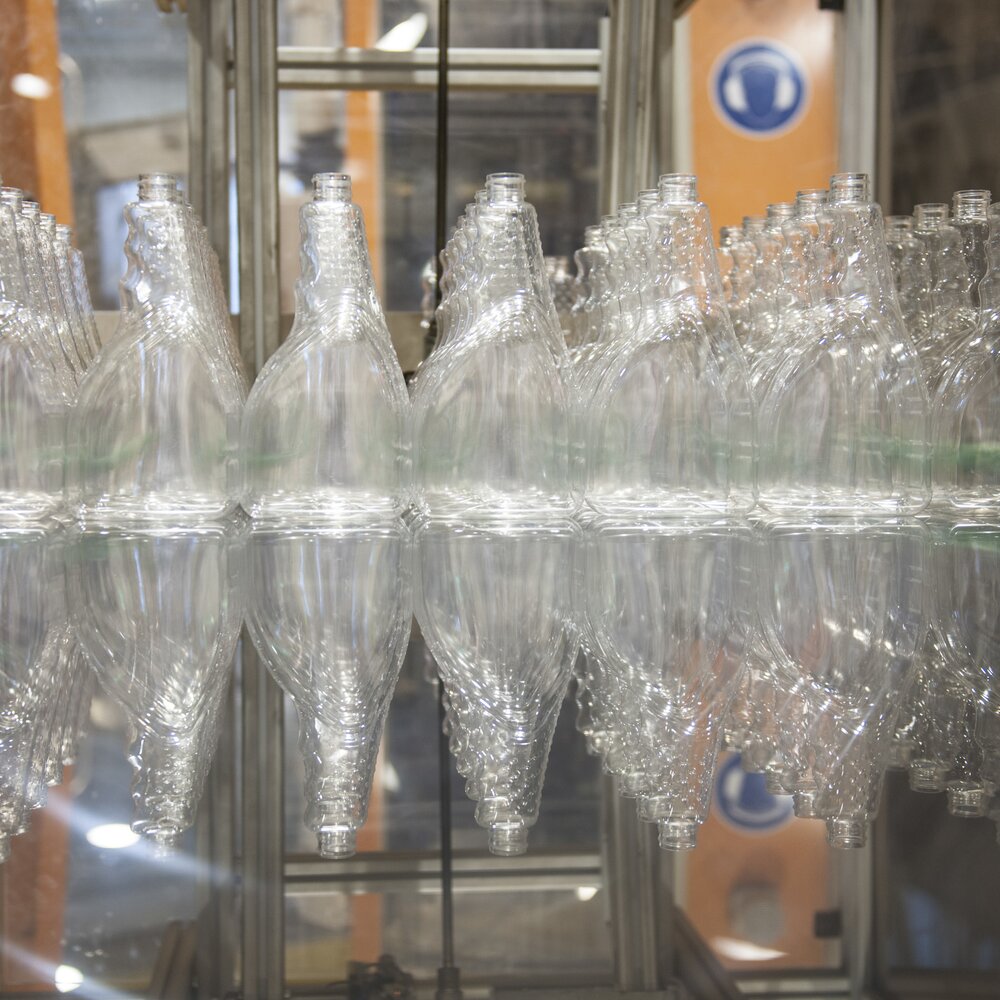
Injection stretch blow molding
Injection stretch blow molding is used to produce hollow items made of plastic, such as PET bottles. The technology stands out first and foremost for the precisely shaped neck sections, optimal surface quality, and strength of the resulting end products.
Materials used: primarily PET and PP.
Products: 5-gallon water bottles (BPA-free), spice jars, tubes for mustard, baby bottles (BPA-free)
Established method for producing hollow items
During injection stretch blow molding, the granulate is smelted and injection molded into a preform that already has the finished opening of the product. The preform is then stretched forward in a second tool and, using high pressure, blown into the blow molds for the finished product. At Greiner Packaging, injection and blowing are done as part of a process (single-step process), so that the residual heat in the preform can be used efficiently.Materials used: primarily PET and PP.
Products: 5-gallon water bottles (BPA-free), spice jars, tubes for mustard, baby bottles (BPA-free)
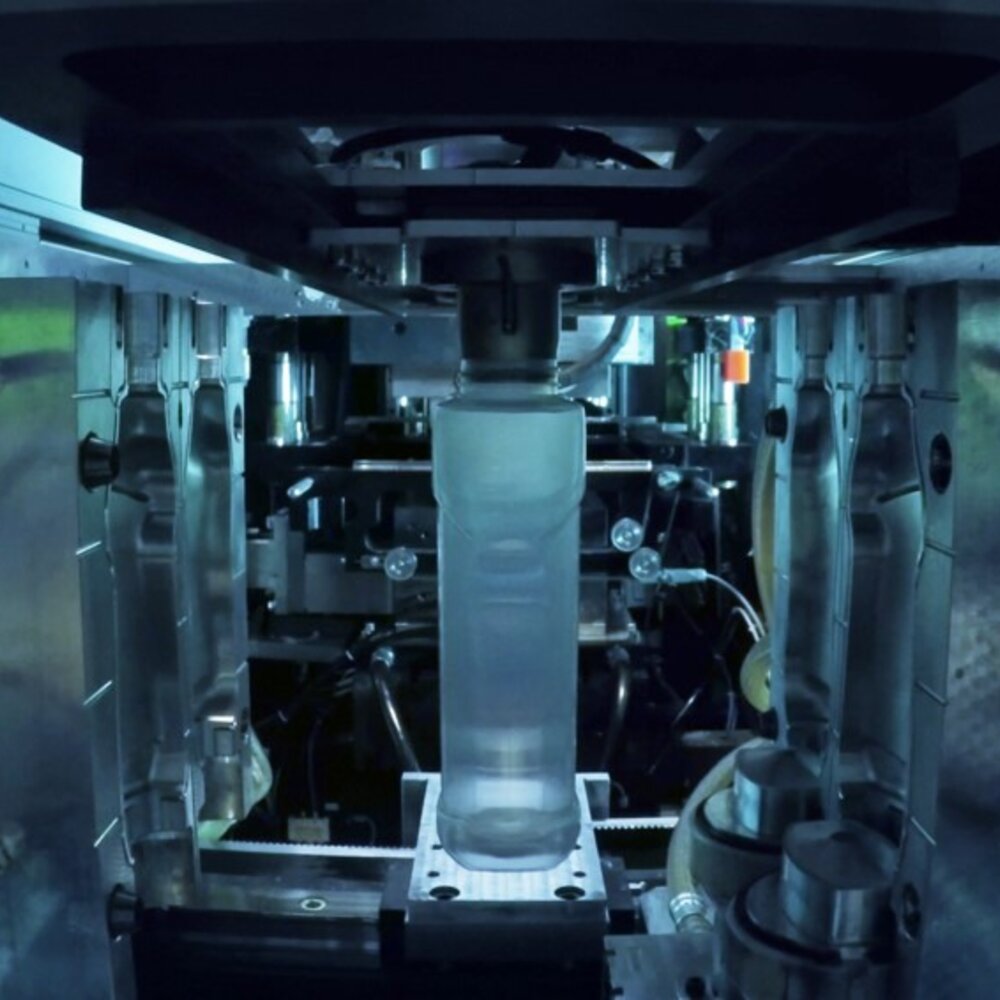
Kavoblow technology
Greiner Packaging has developed an innovative injection stretch blow molding machine, the Kavoblow technology, which combines high flexibility with maximum productivity. The linear movement of the preform, from the injection molding machine to the blowing station, makes it possible to use tools on this machine with a higher number of cavities. Kavoblow allows packaging with non-circular and off-center openings as well as custom color designs to be produced in a wide variety of materials.
Materials used: PET, PP
Products: primarily honey, sauce, and mouthwash bottles, cleaning agents, etc.
Materials used: PET, PP
Products: primarily honey, sauce, and mouthwash bottles, cleaning agents, etc.
Mix & match meal box

Discover our ultimate reusable packaging for restaurants.
Learn more now!